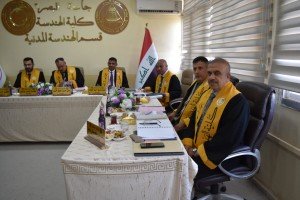
I researched a doctoral thesis at the College of Engineering at the University of Basrah (analysis of specific elements and optimization of wire drawing processes without the use of templates)
The message presented by the student Rafid Jabbar Muhammad Al-Sakini included the design and construction of a special machine for the drawing process without the use of a template for the purpose of carrying out a series of practical experiments on a stainless steel wire with initial diameters of 1.6 mm and 2 mm. The speed of the wire feeding and drawing was controlled by a three-limit PID controller.
During the experimental experiments, the effect of the following factors on the drawing process without a template was studied: process speed, amount of heat supplied, width of heating coil, distance between heating and cooling unit. Also, an artificial neural network model was developed based on the data obtained from practical experiments for the purpose of predicting the behavior of the drawing process without a template.
The thesis aims to draw wires without a template, as it is considered an innovative technology that originated and developed in conjunction with the development of the concept of super-plasticity for metals. This technique takes advantage of local heating in a specific area of a wire or tube to a certain temperature, usually greater than or equal to forty percent of the melting temperature of the material On the absolute scale for the purpose of reducing the resistance of the material and increasing its ductility for the purpose of ease of formation
The thesis concluded that an area reduction rate of 41% and 38% was achieved for the wire with initial diameter of 2 mm and 1.6 mm, respectively. The obtained results revealed that the tensile strength, modulation stress, strain, strain rate, temperature distribution and final wire diameter were affected by the changes of both process speed, heating coil width, amount of heat supplied and the separation distance between heating and cooling unit.